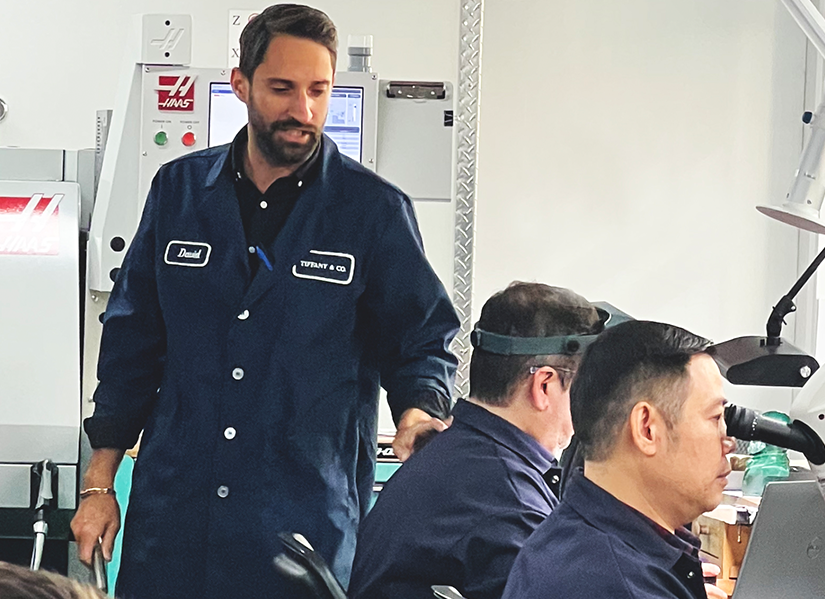
Victoria Aldred, 13 September, 2023
From the soccer pitch to the heart of Tiffany & Co.'s Design and Innovation Workshop, David's journey is nothing short of exceptional. His roots in professional soccer, have helped to forge a relentless pursuit of excellence that now propels his accomplishments in jewellery design and mechanical engineering. Explore with us the key highlights of his role, the evolving landscape of jewellery design, and how he masterfully combines creativity and engineering. David's story is a testament to his remarkable adaptability and unwavering commitment to success.
As the Senior Director – Design and Innovation Workshop at Tiffany and Co. what aspects of your role do you enjoy the most?
There are a lot of different aspects that I really enjoy but if I was to narrow it down to a few they would be:
- Problem Solving – I spend a big portion of my job doing Design for Manufacturability (DFM). Taking initial design concepts and sketches and bringing them to life.
- Leading – I was approached by Tiffany & Co. to build a team from the ground up when I came over to the company and, in 5 years I’ve been able to create my own team. This has been very rewarding seeing the growth over the years and watching my team evolve, learn, and succeed.
- Contract Manufacturing Partnerships – We have hundreds of manufacturing partners around the world, including our own internal team, and it’s our job to understand all the different suppliers, technical capabilities, and capacity. Managing what designs go where to ensure the best quality product.
In a rapidly evolving technological landscape, how do you see the role of mechanical engineering in jewellery design evolving in the future?
In larger jewellery companies there has been a big push for mechanical engineers over the past 10 years. It is no different to any larger scale manufacturing operation. When you are making thousands of parts across multiply suppliers there is a need for consistency, control, and clear documentation.
I only see this increasingly becoming more of a need in the future. We are constantly pushing the boundaries in new manufacturing methods, systems and equipment - trying to stay relevant. Finding efficiencies in the way we develop and/or manufacture product is a big focus for us at Tiffany & Co.
How do you bridge the gap between design vision and engineering feasibility while collaborating with colleagues from diverse backgrounds?
We keep our teams in separate spaces (Design & Engineering) for multiple reasons. The design team needs to be allowed to be creative and not be affected by the potential challenges in manufacturing, we do not want to curb that process.
This is also goes the same for the engineering team – however we do have key phases in our development timelines where the teams come together throughout the process and share their DFM challenges – it is very collaborative process when we need important decisions made to move product forward.
How does your design and engineering background help you anticipate and respond to jewellery trends and consumer preferences, ensuring your designs are both timeless and contemporary?
I am fortunate that I have both backgrounds. Jewellery at the end of the day is a piece of art, so respecting the design when in the manufacturing (MFG) process is really important.
I find when recruiting I am looking for creative engineers, and it’s not easy to find as they are two conflicting ways of thought. Typically, the engineering mindset it to make the product simple and straight forward to the MFG process for multiple reasons. Being respectful and appreciating the design is sometimes very difficult to do when working with complex geometries - that is the creative problem solving my team does every day.
How do you approach training, mentorship, and operational planning to enhance the overall quality and outcomes of your team's efforts?
We have a very robust onboarding program for all new employees, they spend a lot of time in factories learning our product, our process, and our company history. To contribute in a positive way those fundamentals are important. This process can take from three months or even six months depending on the individual.
Coming from a rural town of Ayr in Queensland what inspired you move initially to Brisbane to study, and now work in New York City?
So, I left home when I was 14 years old to move to Brisbane for high school, as I was in a soccer excellence program. I then moved to Italy when I was 16 to play professional soccer. I was in Italy for over five years before suffering two bad knee injuries that forced me to stop playing at a very young age. I then moved back to Brisbane and went to university as a mature age student. Once I graduated, I moved to New York City for a life change and challenge, and New York City is definitely a challenge. The city is extremely ruthless. It’s not for everyone.
While studying at QUT, you combined two different study areas of Industrial Design and Mechanical Engineering. What prompted you to do that?
I loved Industrial Design, but the further I got into my degree I found myself wanting to understand more and more how things were made. I felt like to be successful in Industrial Design I needed a balance of the two. Again, this isn’t for everyone as they are two conflicting ways of thinking, but for me it just made sense. I am also glad I did it, as it has given me such a unique point of difference throughout my career.
Have you always wanted to work in New York City? What steps did you take to get there?
Definitely not, I had friends in New York City that I went to visit, and I fell in love with the city and the energy. It just seemed like it would be a good fit for me to grow and build that next chapter of my life. I didn’t expect to stay for longer than a year or two before coming back to Australia. 13 years later, I am still here.
I would love to move back home one of these days, but you never know. Right now, I am bicoastal. I spend half my time in New York City and half in Los Angeles.
What advice would you offer fellow QUT alumni aspiring to excel in leadership within product design, innovation, and high-end manufacturing?
I think the hardest part is getting your opportunity. Don’t be caught up in getting your dream job at the beginning. It’s all about learning and becoming a professional, slowly building your skills and understanding exactly what you want to do within your space. Once you have that foundation and confidence, you just need to work hard. It takes time, dedication, and patience.
What is one skill you couldn’t live without and why?
Communicating ideas through sketching. A picture speaks a thousand words. Being able to communicate through pictures breaks down language barriers, it’s by far the most important and powerful tool in my industry.
Do you have a question for David? Connect with him on LinkedIn.