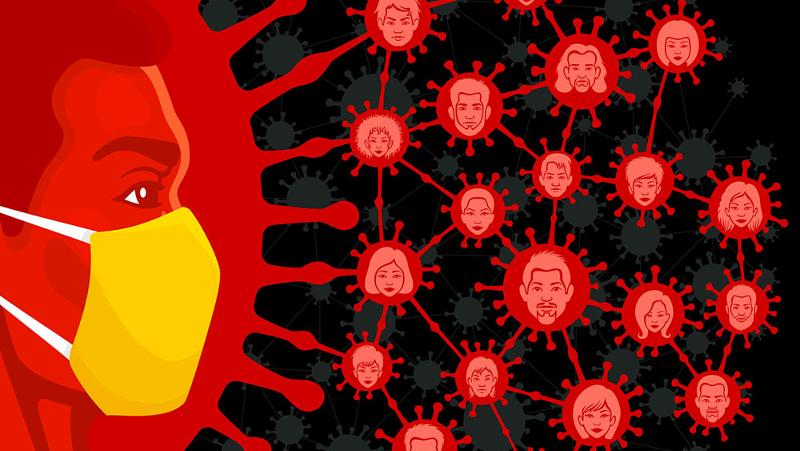
Scientists around the world are scrambling to adapt their research to find solutions to the many problems raised by the Covid-19 pandemic sweeping the world, not the least being a face mask shortage.
- A new material created by QUT scientists is very effective at removing particles smaller than 100 nanometres, which is in the range of a virus
- Material is easier to breathe through than high-quality face masks - important for people with existing respiratory issues
- Can be quickly made in large quantities using simple equipment, it is biodegradable and made from waste plant material
- Thoroughly tested and compared with high-quality commercially available
QUT process engineer Dr Thomas Rainey and his research team are stepping up work on a nanoparticle-removing new material they were developing for biodegradable anti-pollution masks.
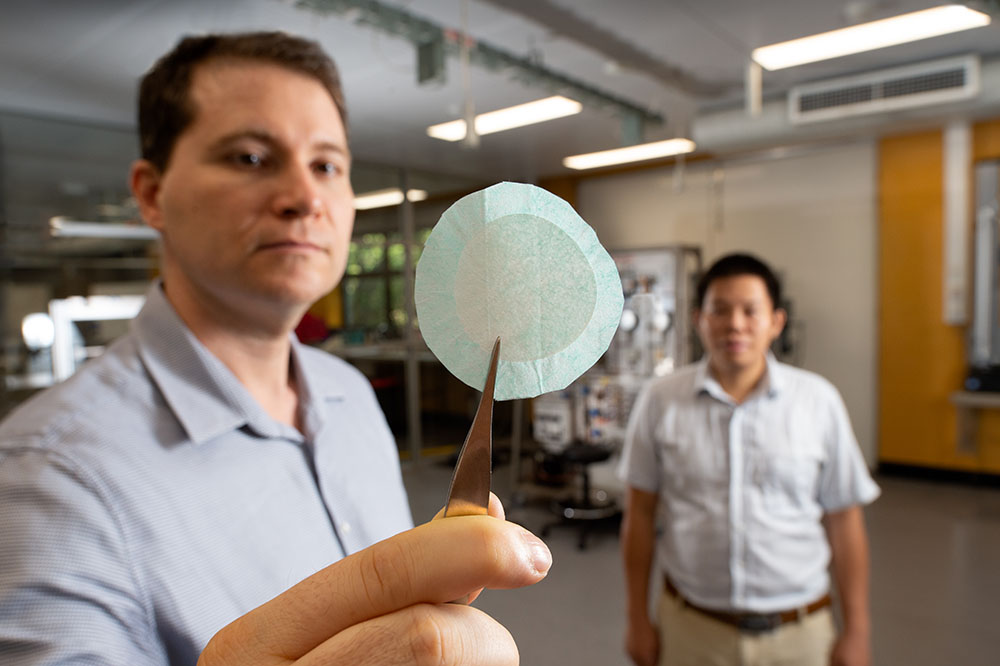
“We have developed and tested a highly breathable nanocellulose material that can remove particles smaller than 100 nanometres, the size of viruses,” Dr Rainey said.
“I see many people wearing masks which are not tested for viruses. We have tested this material thoroughly and found it to be more efficient in its ability to remove virus-size nanoparticles than the high-quality commercially available masks we tested and compared it with.”
Dr Rainey said the team also tested the new material for breathability.
“By breathability we mean the pressure or effort the wearer has to use to breathe through the mask. The higher the breathability the greater the comfort and reduction in fatigue,” he said.
“This is an important factor for people who have to wear masks for long periods or those with existing respiratory conditions.
“Our tests showed the new material was more breathable than commercial face masks, including surgical masks.
“This new material has excellent breathability, and greater ability to remove the smallest particles.”
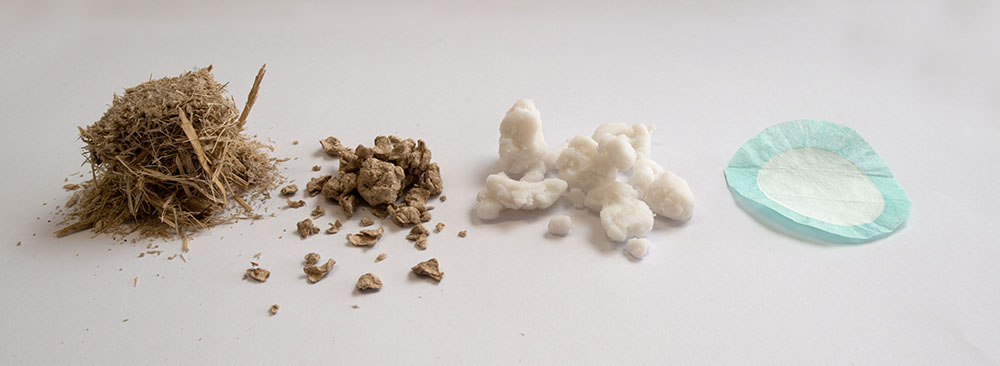
Dr Rainey said the material could be used as a disposable filter cartridge in face masks.
“This material would be relatively inexpensive to produce and would therefore be suitable for single-use.
“The cellulose nanofiber component is made from waste plant material such as sugar cane bagasse and other agricultural waste products and is, therefore, biodegradable. It can be made using relatively simple equipment, and so we can quickly produce large quantities of the material.”
“We have established proof of concept as a nanoparticulate filtration material and we are currently seeking industry partners.”
QUT Media contacts:
Niki Widdowson, 07 3138 2999 or n.widdowson@qut.edu.au
After hours: Rose Trapnell, 0407 585 901 or media@qut.edu.au.